The Future Of 3D Printing: Innovations On The Horizon
Are you ready for a glimpse into the future? 3D printing has already revolutionized the manufacturing industry, but the innovations on the horizon are even more exciting. From printing entire houses to creating human organs, the possibilities seem endless.
In this article, we will explore the future of 3D printing and the groundbreaking advancements that are just around the corner. Get ready to be amazed as we delve into the world of cutting-edge technology and discover how it will shape our lives in the years to come.
So, buckle up and prepare to be transported into a world where imagination meets reality, where objects can be printed with astonishing precision and complexity. The future of 3D printing is here, and it promises to change the way we live, work, and create.
What Is 3D Printing?
3D printing, also known as additive manufacturing, is an innovative technology that allows for the creation of three-dimensional objects through layer-by-layer printing. Instead of removing material from a solid block or mold, like in traditional manufacturing methods, 3D printing builds objects by adding successive layers of material.
The principles behind 3D printing are based on the additive manufacturing process. A digital design is created using computer-aided design (CAD) software, which is then sliced into thin cross-sectional layers. These layers are then sent to the 3D printer, which uses materials such as plastics, metals, or even biological substances to build the object layer by layer. The layers are fused together to create a solid, physical object that matches the digital design.

Advantages Of Using 3D Printing Technology
3D printing technology offers a multitude of advantages that revolutionize various industries. One key advantage is rapid prototyping, which allows for the quick and cost-effective production of prototypes. This enables designers and engineers to iterate and test their designs more efficiently, accelerating the product development process.
Another advantage is the utilization of real materials. Unlike traditional manufacturing methods, 3D printing enables the production of parts using the same materials that will be used in the final product. This provides valuable insights into the functional performance and durability of the design.
Cost savings are also a significant advantage of 3D printing. By eliminating the need for expensive molds or tooling, manufacturers can significantly reduce production costs. Moreover, 3D printing allows for on-demand manufacturing, eliminating the need for large inventories and reducing the risk of excess stock.
Furthermore, 3D printing is becoming smarter by integrating sensors, cameras, algorithms, artificial intelligence, and machine learning. This integration increases accuracy and efficiency by enabling the printers to detect errors during the printing process. It also enables the optimization of print settings to achieve the best possible results.
Smart 3D printers are also capable of recording and adjusting the printing process in real-time. This ensures consistent and precise printing, minimizing waste and reducing the chances of errors.
Applications Of 3D Printing
3D printing technology has revolutionized the manufacturing industry, offering a wide range of applications that were previously unimaginable. The ability to create three-dimensional models and end-use parts with precision and speed has opened up endless possibilities for businesses across various sectors. One of the most significant advantages of 3D printing is its versatility, as it can be applied to different industries such as automotive, medical, aerospace, and more. Rapid prototyping, which allows for quick iterations and design improvements, is a leading application of 3D printing.
Automotive Industry
In the automotive industry, 3D printing technology has revolutionized the way various applications are approached. From rapid prototyping to the production of high-performance parts, tooling and manufacturing aids, and even on-demand manufacturing of replacement and spare parts, the utilization of 3D printing has significantly impacted the sector.
One of the main advantages of 3D printing in the automotive industry is its ability to reduce costs and lead times. Traditionally, outsourcing the production of parts could take weeks or even months. However, with 3D printing, manufacturers can significantly cut down on lead times, sometimes by up to 90%. This not only allows for faster prototyping and product development but also increases overall operational efficiency.
3D printing enables the production of complex geometries and intricate designs that would otherwise be challenging or impossible with traditional manufacturing methods. This has led to the creation of high-performance parts that enhance the overall performance and efficiency of vehicles.
Medical Field
3D printing technology has revolutionized the medical field, offering innovative solutions for fabricating biomedical implants, producing surgical tools, and enabling individualized patient care.
In the realm of tissue repair and orthopedics, 3D printing allows for the creation of custom implants that perfectly fit a patient’s unique anatomy. This personalized approach enhances patient outcomes and reduces the risk of complications. Surgeons can now design and produce implants, such as cranial and facial implants, spinal implants, and joint replacements, tailored to the patient’s specific needs. This level of customization ensures better functionality and improved patient comfort.
3D printing enables the fabrication of surgical tools that are highly precise and tailored to specific procedures. Surgeons can utilize patient-specific anatomical data to create 3D models, allowing them to practice complex operations before performing them on the actual patient. This enhances surgical accuracy, reduces operative time, and minimizes potential risks.
Aerospace & Defense Industry
3D printing technology has made significant strides in revolutionizing the Aerospace & Defense industry. This cutting-edge innovation offers several advancements, including the fabrication of complex engine parts with lower weight and reduced life-cycle costs.
The aerospace industry has long sought to optimize the weight of aircraft components to improve fuel efficiency and overall performance. 3D printing, also known as additive manufacturing (AM), allows for the creation of intricate and lightweight components that were previously impossible to achieve using traditional manufacturing methods. By utilizing AM techniques, aerospace manufacturers can design and produce engine parts with intricate geometries, consolidating multiple components into a single piece. This not only reduces weight but also decreases the need for assembly, resulting in streamlined manufacturing processes and reduced overall costs.
The potential for on-demand and on-site fabrication has immense implications for astronauts in space. With access to 3D printing capabilities, astronauts can manufacture necessary parts for space station repair or maintenance, eliminating the need for costly resupply missions from Earth. This on-demand fabrication capability ensures that space stations remain operational and functional, while also minimizing the logistical challenges and costs associated with supply chain management in space.
Consumer Goods & Retail Industry
3D printing technology has had a significant impact on the consumer goods and retail industry, revolutionizing product design, customization, and manufacturing processes. This innovative technology allows retailers to create products on-demand, reducing inventory costs and the risks associated with overstocking.
3D printing in this industry is its ability to produce prototypes quickly and cost-effectively. Traditional manufacturing methods often require expensive tooling and longer lead times for prototype development. With 3D printing, retailers can rapidly iterate and test new designs, reducing time-to-market and enabling a faster response to consumer demands.
3D printing enables customization like never before. Consumers can now personalize products by selecting specific colors, shapes, or even adding their own designs. This level of customization enhances customer satisfaction and allows retailers to offer unique and personalized products, setting them apart from competitors.
3D printing opens up avenues for the production of limited edition items. Retailers can create exclusive and highly desirable products that cater to niche markets. This approach adds value to the consumer experience and creates a sense of scarcity, driving demand and increasing customer loyalty.
Manufacturing & Construction Industry
The role of 3D printing technology in the manufacturing and construction industry is revolutionizing the way products are designed, prototyped, and produced. With its ability to create complex geometries and structures, 3D printing is providing a new level of precision and intricacy in manufacturing.
Some of the key players in the industry include 3D Systems, Form Labs, Stratasys, HP, and Desktop Metal. These companies are at the forefront of developing and advancing 3D printing technology, pushing the boundaries of what is possible in manufacturing and construction. With their innovative solutions, they are driving the adoption of 3D printing in the industry and shaping the future of manufacturing.
Different Types Of 3D Printers
There are several different types of 3D printers available today, each with its own unique characteristics and capabilities. As technology continues to advance, new types of 3D printers, such as those using metal additive manufacturing or bioprinting techniques, are also emerging, further expanding the possibilities and applications of 3D printing.
Fused Deposition Modeling (FDM) Printer
The Fused Deposition Modeling (FDM) printer is one of the most commonly used types of 3D printers in the field of additive manufacturing. It works by melting a thermoplastic filament and extruding it layer by layer to create a solid object.
One of the key advantages of the FDM printer is its functionality. It allows for the creation of complex geometries and intricate designs, making it ideal for rapid prototyping and small-scale production. The FDM printer is also relatively affordable and accessible, making it a popular choice for hobbyists and small businesses.
However, it’s important to note that the FDM printer does have certain limitations. The layer-by-layer process can result in visible layer lines on the final printed object, which may require post-processing to achieve a smoother finish. Additionally, the strength and durability of the printed objects may be limited compared to those produced using other 3D printing technologies.
Despite these limitations, the FDM printer remains an important tool in the world of 3D printing. With ongoing advancements and innovations in additive manufacturing technology, we can expect to see further improvements in the functionality and capabilities of the FDM printer in the future.
Stereolithography (SLA) Printer
The Stereolithography (SLA) printer is another revolutionary innovation in the field of 3D printing. This cutting-edge technology offers several advantages and benefits that set it apart from other printing techniques.
At the heart of the SLA printer is a liquid resin that is cured layer by layer using a UV light source. This unique working principle allows for incredible precision and accuracy in printing. The liquid resin solidifies when exposed to the UV light printing, resulting in a fully formed object with high detail and resolution.
Digital Light Processing Printer (DLP)
The Digital Light Processing Printer (DLP) is a revolutionary 3D printing technology that offers numerous benefits in the world of additive manufacturing. Similar to SLA printers, DLP printers utilize a liquid resin to create objects layer by layer. However, the key difference lies in the curing process.
DLP printers employ a digital micromirror device (DMD) and a projector to cure the liquid resin. The projected light creates high-intensity beams that selectively solidify the resin, resulting in precise and high-resolution prints. This technology allows for faster printing speeds compared to traditional SLA printers.
Selective Laser Sintering (SLS) Printer
Selective Laser Sintering (SLS) is a 3D printing technology that utilizes a high-powered laser to selectively fuse powdered materials together to create solid objects. The SLS printer works by spreading a thin layer of powdered material onto a build platform. The laser then scans across the powder, selectively melting or sintering the particles together according to the digital design.
In the medical field, SLS printing has revolutionized the production of prosthetics, implants, and surgical instruments. The ability to create complex and custom shapes with high precision has made SLS-printed parts an ideal choice in personalized healthcare. Additionally, SLS printers are capable of printing with biocompatible materials, allowing for the creation of implants that integrate seamlessly with the human body.
Metal Additive Manufacturing (AM) Printers
Metal Additive Manufacturing (AM) printers, also known as metal 3D printers, are revolutionizing the manufacturing industry by enabling the production of complex metal parts with high precision. There are several types of metal AM printers, each with its own unique functions and capabilities.
One type of metal AM printer is the Powder Bed Fusion (PBF) printer. PBF printers use a laser or electron beam to selectively melt metal powder, layer by layer, to create a solid metal part. This method offers high resolution and excellent mechanical properties, making it suitable for aerospace and automotive applications.
Another type of metal AM printer is the Directed Energy Deposition (DED) printer. DED printers deposit metal powder or wire onto a substrate and then melt it with a laser or electron beam. This technique allows for the fabrication of large-scale parts and the use of multiple materials in a single build, making it ideal for the repair and modification of existing metal components.
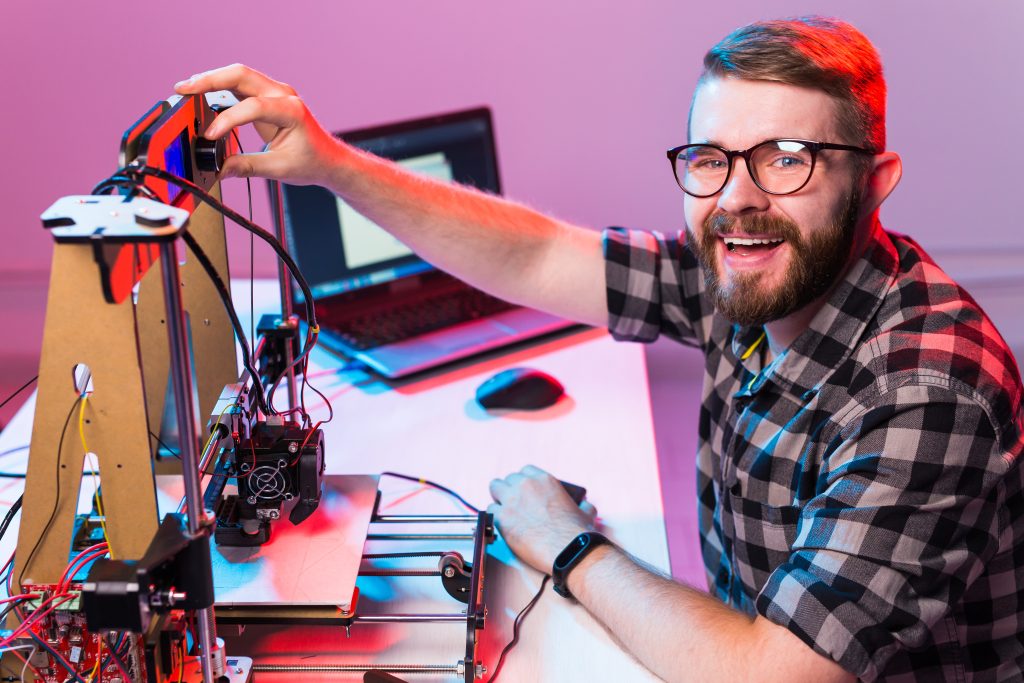
Conclusion
In conclusion, the future of 3D printing is incredibly promising. The advancements and innovations that are on the horizon are set to revolutionize various industries and improve our daily lives in ways we can’t even imagine.
From healthcare to manufacturing, 3D printing is poised to play a significant role in shaping the future. The ability to create complex structures, customized products, and even human organs has the potential to transform the way we approach healthcare and create solutions for medical challenges.
Furthermore, the increasing accessibility and affordability of 3D printers will empower individuals and small businesses to unleash their creativity and bring their ideas to life. This democratization of manufacturing will lead to a surge in innovation and entrepreneurship, as more people have the means to turn their concepts into tangible products.
As with any technology, there are challenges and obstacles to overcome. Issues such as intellectual property rights, quality control, and the need for standardized materials still need to be addressed. However, the potential benefits far outweigh these challenges, and the ongoing research and development in the field are continuously pushing the boundaries of what is possible.
In conclusion, the future of 3D printing is bright and filled with endless possibilities. It has the potential to disrupt industries, transform healthcare, empower individuals, and contribute to a more sustainable world. As we embark on this exciting journey, it is essential to embrace the potential of 3D printing and continue to explore the innovations on the horizon.
Leave feedback about this